Landfill Gas
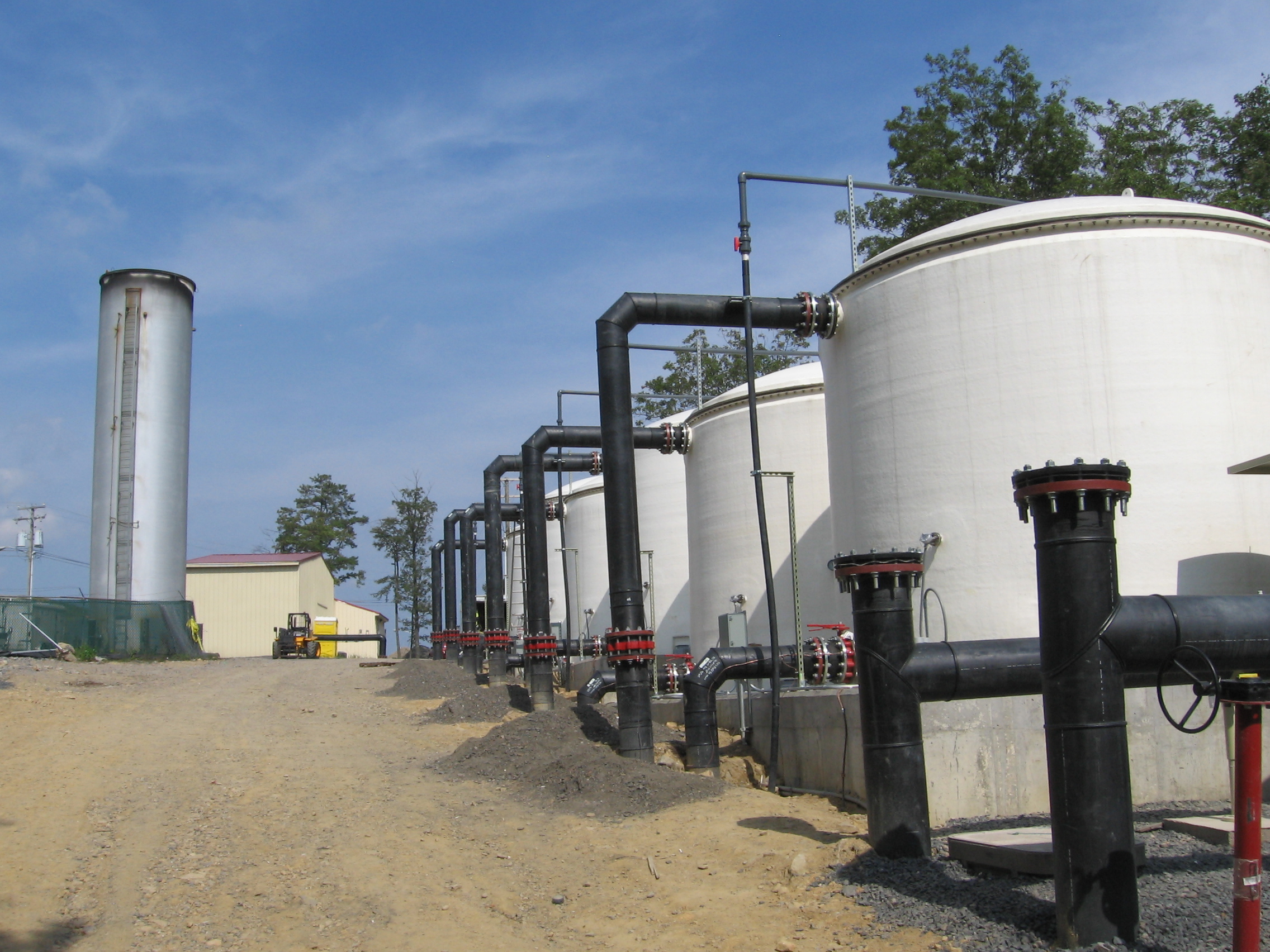
H2S Treatment for Landfill Gas
MV Technologies H2 removal solutions are in use at Landfill sites to treat landfill gas for SO2 emissions compliance as well as use as fuel for boilers or other process equipment, to power generator sets, or to convert to CNG either directly or through utility pipeline.
Odor emissions often are managed at Landfill sites through use of wells, exhaust systems and flares to treat the gases generated in the landfill mass. In certain conditions, the gas that is burned in the flare contains enough H2S to yield over the limit for SO2 conditions in the flare exhaust. Compliance requires reducing the H2S levels before combustion.
Landfill sites can collect the methane-bearing gas produced by bacterial action on the landfill material for use as fuel for boilers or other process equipment, to power generator sets, or to convert to CNG either directly or through utility pipeline transmission.
When used as a fuel source, the presence of H2S in the biogas will have a damaging effect on reciprocating or turbine engine life, increase maintenance costs, and shorten time between rebuilds. Generator set manufacturers have begun setting limits on H2S concentrations as part of their conditions imposed on the user to maintain warranty coverage.
Exhaust limits on SO2 emissions may require H2S reduction prior to combustion even at a flare. If the LFG is converted to CNG, those specifications include low limits on H2S. When the gas is transported via a utility pipeline to a CNG compression station, even lower pipeline specifications will have priority.
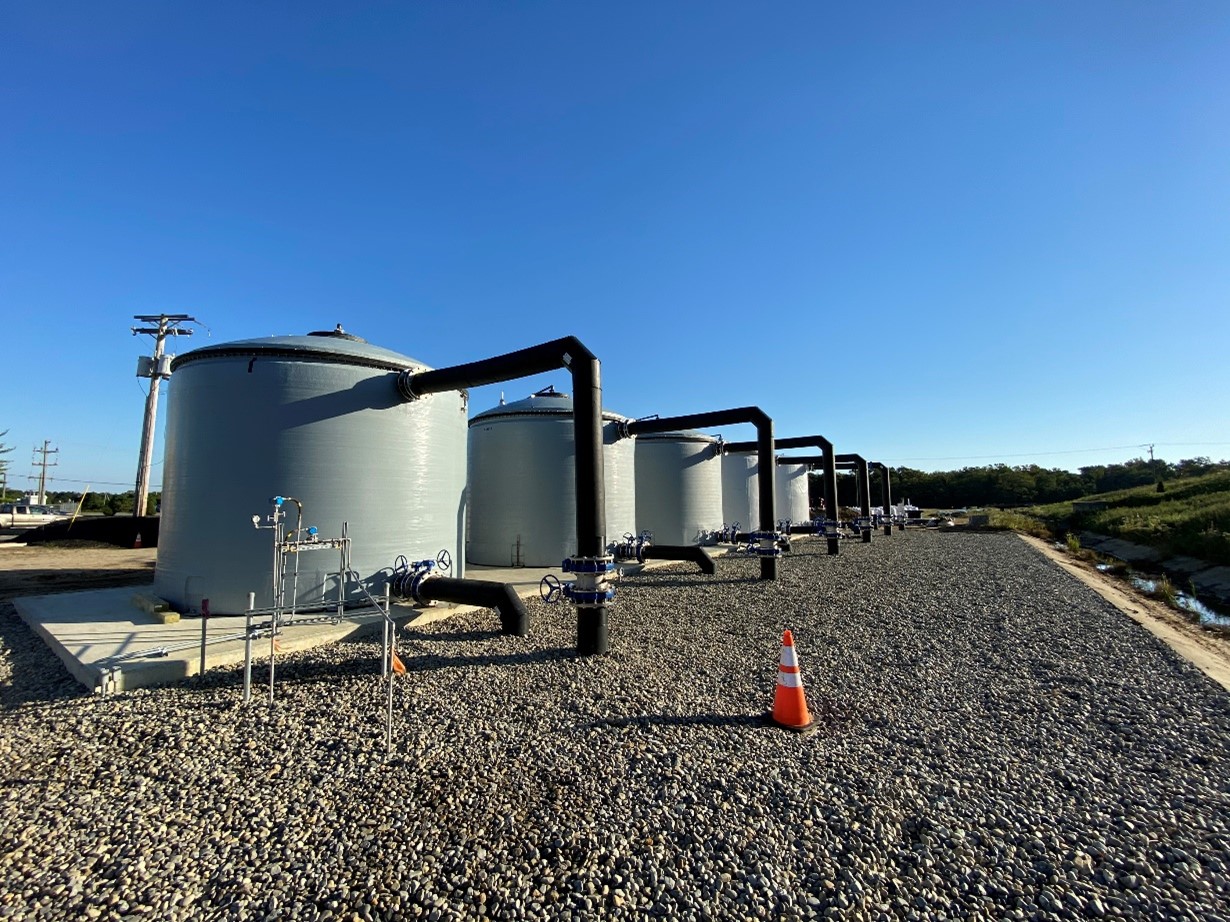
Typical User Conditions
Flow rates are typically mid-range to high, 1500scfm to more than 5000scfm. H2S concentrations are typically not extreme, running between 500 and 2000ppm. Importantly, concentrations will vary widely according to landfill cell management.
MVTechnologies H2SPlus systems and SulfAx Systems deliver superior value against these requirements.
Additionally, in evaluating H2S treatment approaches, an important metric to consider is the Total Cost of Ownership (TCO).
The TCO includes capital cost such as the vessel size, pumps and installation costs, and the operating costs, largely determined by media life and resulting time between replacement — itself a function of biogas flow rate and H2S concentration. MV’s enhanced iron sponge (BAM) media is guaranteed to remove up to 13 pounds of H2S per cubic foot, one of the highest removal efficiencies in the industry.
The TCO includes capital cost such as the vessel size, pumps and installation costs, and the operating costs, largely determined by media life and resulting time between replacement — itself a function of biogas flow rate and H2S concentration. MV’s enhanced iron sponge (BAM) media is guaranteed to remove up to 13 pounds of H2S per cubic foot, one of the highest removal efficiencies in the industry.
Cost elements often overlooked during comparison of H2S treatment approaches
- Power costs – increase in pressure drop can result in increase in power costs
- Lost Revenue due to system downtime – maintenance/media changes
- Replacement of proprietary nutrients and/or chemical/caustic
- The costs of testing for warranty or regulatory requirements
- Operator attention time – it is not “free”
Frequently Asked Questions
Landfill Gas, or LFG, is produced when organic materials begin to decompose via a process called aerobic decomposition. LFG is typically made up of CO2, or carbon dioxide, and CH4, or methane. In most cases, landfill gas will also include trace amounts of additional gases that may be potentially harmful to the surrounding environment, such as H2S.
Various sensors and gas analyzers designed for landfill environments can detect and measure H2S levels in landfill gas. MV Technologies can assist with measuring and detecting potential H2S in a safe and secure environment while providing real-time data on concentration levels and potential surrounding risks.
Removing H2S from landfill gas is essential as the gas itself is toxic and can increase surrounding air pollution. Additionally, H2S is known to be corrosive and toxic, which can damage surrounding equipment, effectively shortening the lifespan of any equipment utilized at a landfill location.
The concentration level of H2S will vary from landfill to landfill based on a landfill’s location, regulations, upkeep, and overall landfill cell management strategies in place. In most landfills, it is expected that H2S concentration levels read between 500 and 2000 ppm.
When attempting to remove and eliminate H2S from landfill gas, an iron sponge or B.A.M. iron sponge media can be used. Activated carbon and/or granular media may also be suggested in some cases, depending on the specifications and demands of a particular landfill location and the concentration level of H2S at that landfill.
Removing H2S buildup from landfill gas will ensure your plant, facility, or warehouse abides by current laws and regulations that may be in effect in your state, region, or particular industry. Regulation and environmental compliance can reduce the risks of operational shutdowns, unexpected inspections, and exuberant fines or fees.
When H2S is permitted into the atmosphere unfettered and without monitoring or removal solutions, it will likely lead to the corroding of various pieces of equipment. Damage to generators, turbines, and even various engines is not uncommon with overexposure to H2S in a landfill.
Once a landfill location has been thoroughly inspected, assessed, and analyzed for H2S concentration level, a particular media that is suitable for the removal of the gas will be used in a specific vessel. The media chosen will then interact directly with the H2S that is found in the emissions of the surrounding atmosphere. Once the chosen media, such as B.A.M. iron sponge, standard iron sponge, activated carbon, or granular media, comes in contact with the H2S, it will immediately react, converting the H2S into non-toxic compounds. For instance, when iron sponge media is applied, the non-toxic compound that will take the place of H2S is iron sulfide.